Beta Prime Industry
Top Entry Agitators
Top Entry Agitators
7*24 Online!
sale@betaprimeindustry.com
WA:+86189 8077 6200
TT, Paypal, LC Payment Acceptable.
Contact us to get discounts.
Couldn't load pickup availability
Top Entry Mixers, commonly referred to as "agitators," are widely used in various industrial fields and are the preferred mixers for batching tanks, continuous mixing tanks, and semi-continuous mixing tanks. Different seal types provided include: Open tank | Pressurized cover seal | Lip seal | Steam seal | Single-layer seal | Double-layer seal | Magnetic seal
Structural materials
Stainless steel | Chromenickel iron alloy | Monel alloy | Hastelloy alloy | Dual-refined steel | Titanium alloy | Lined or unlined carbon steel (with rubber lining, FRP, PVDF, PTFE, Halar, etc.)
Application areas
Chemical | Mining and metals | Paints, resins, and inks | Pharmaceuticals and biotechnology | Food and beverages | Sugar | Wastewater treatment plants
Design and Operation
The most basic configuration of the agitator includes the prime mover, i.e., the motor connected to the reducer to provide the necessary torque. The connection of the motor and gear device to the agitator shaft in the container is typically isolated using various paint arrangements.
The type of sealing device will be determined based on the nature of the fluid and the required level of isolation for plant and process safety. The shaft inside the tank typically has single or multi-stage impellers to achieve fluid motion. The selection of impellers and their rotational speed is determined by application engineers based on process requirements. Mechanical components such as bearings, shaft size, couplings, etc., are then selected reasonably to ensure smooth operation.
The seal configuration and structural materials of top entry agitators may vary, and some may even be directly driven by the motor instead of through a reducer. Most of these agitators are installed vertically at the center of the tank. However, depending on process requirements, eccentric or tilted installation methods or a combination of both may be used.
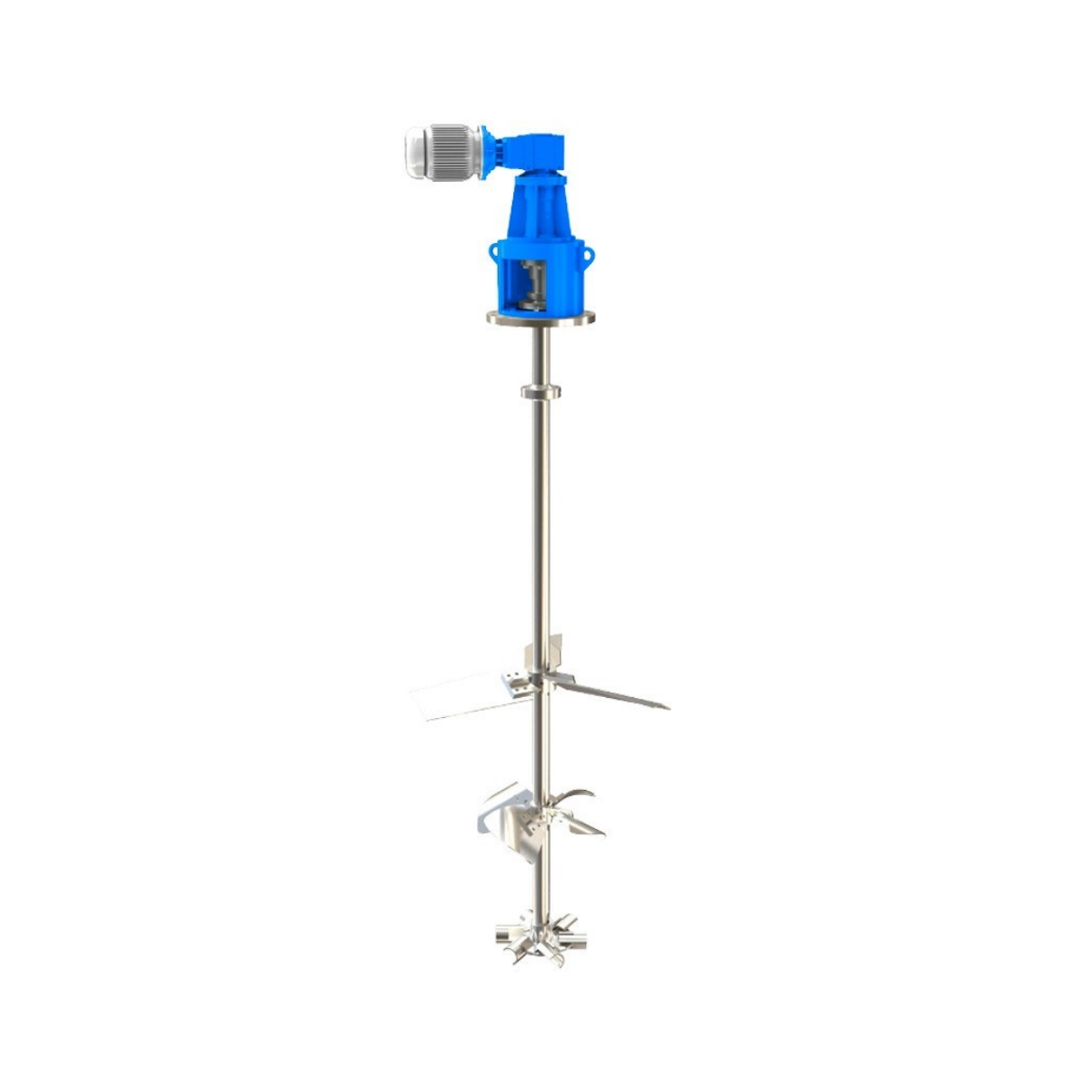
